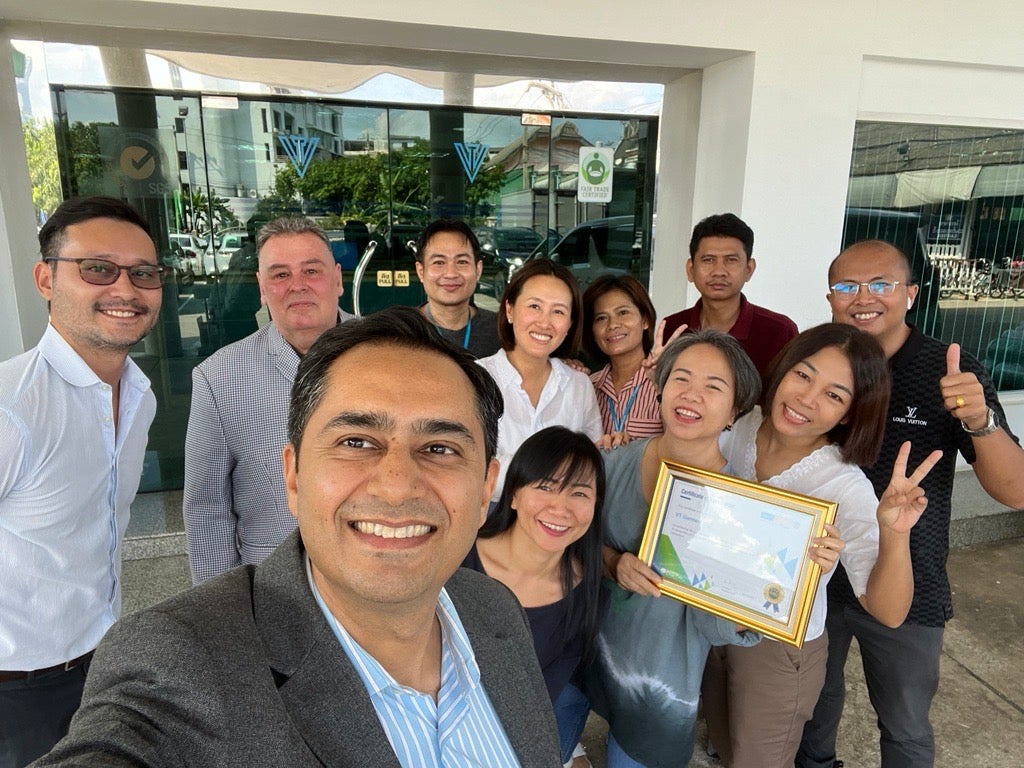
Coats Digital is delighted to announce that global apparel manufacturing powerhouse VT Garment Co. Ltd. has become its first customer partner to achieve GSD Excellence Gold Certification as part of its new GSD Programme. The initiative has been launched to empower manufacturers to reach new levels of efficiency and sustainability through best practices and GSD’s data-driven methodology – helping them meet increasingly rigorous standards set by global brands.
Since its adoption of GSDCost, VT Garment has boosted sales orders by 30%, improved its on-time delivery performance by 13%, increased production efficiencies by up to 30% and significantly reduced unnecessary overtime, air freight, machine rental and material costs.
VT Garment (VTG) is a leading designer and manufacturer of sustainable sportswear and outerwear, renowned for its award-winning quality and craftsmanship. As one of the largest Fair Trade-certified factories globally, VTG advocates for better wages and working conditions, producing durable outerwear and sportswear from sustainable materials while promoting local sustainability and environmental protection.
VTG has been at the forefront of Thailand’s textile manufacturing innovation, implementing enterprise resource planning, product lifecycle management solutions, and Industry 4.0-driven digitalization, since 1981. This commitment to innovation and efficiency was recognised with the Thailand Lean Golden Award in 2017 and the GSD Excellence Gold Certification in 2024.
Trusted by renowned brands like Patagonia, Jack Wolfskin, Montbell, and O’Neill, VTG produces up to 180,000 apparel items monthly in its Thailand and Myanmar facilities. Recently, VTG achieved LEED Green Building Platinum certification, highlighting its dedication to sustainability, efficient resource use, waste minimisation, and excellent indoor air quality.
As part of Coats Digital’s goal to drive fashion businesses towards manufacturing excellence, its new GSD Excellence Programme has been designed to help fashion businesses create optimal production environments by promoting industry-leading standards that reduce waste and increase productivity. Through a three-tiered structured framework, the annual accreditation programme helps fashion manufacturers to advance progression from Bronze, to Silver, through to Gold Certification.
Accreditation is based on a company’s GSD practitioner capability; its adoption of GSD methodology on the factory floor measured by the rate of production style adoption; factory benchmarks based on production efficiencies and the consistency and quality of its Standard-Minute-Value (SMV/SAM) data. Accreditation enables supply chain vendors to position themselves as market leaders in manufacturing by creating an optimal and sustainable production environment through best-practice consultation and by optimising the benefits of GSDCost.
Kunal Kapur, managing director, Coats Digital, said: “We are excited to launch the GSD Excellence Rewards & Recognition Programme as it marks a significant step forward in empowering manufacturers to reach new levels of efficiency and sustainability. This programme is transformative for manufacturers and brands alike, fostering transparent benchmarks and advancing supply chain competitiveness. I extend huge congratulations to VT Garment. Attaining Gold status is no easy feat, and VT Garment’s dedication showcases what can be achieved when a company fully embraces GSD methodologies.”
Chalumpon Lotharukpong, managing director, VT Garment, said: “We are all immensely proud to have successfully obtained the highest accolade on Coats Digital’s GSD Excellence Programme with Gold Certification. Achieving this certification is a testament to our unwavering commitment to Lean manufacturing and Kaizen/continuous improvement. At VT Garment, we believe that excellence begins with a solid globally-recognised ‘standard’, and our pursuit of perfection in refining that standard draws upon over 40 years of expertise.”
To secure GSD Excellence Gold Certification, Coats Digital’s team of GSD experts conducted a series of rigorous audits at VT Garment to assess its GSD standards, the precision and consistency of its GSD practitioners, and the direct impact GSD methods were delivering in terms of efficiency improvements.
Tan Demir, professional service director – APAC, Coats Digital, said: “VT Garment delivered such astounding results during our stringent audit assessments that it was immediately awarded GSD Excellence Gold Certification. VT Garment has proven itself a true beacon of superior manufacturing excellence. Its dedication to maintaining precision standards and promoting continuous improvement across its operations sets an inspiring example for the entire fashion industry. VT Garment has clearly demonstrated how GSD methodology can drive tangible and transformative benefits, making it stand out as a premier vendor partner for brands wanting to facilitate real supply chain improvements. We are truly thrilled to see VT Garment becoming the trailblazer for our new GSD Excellence initiative by achieving the highest accreditation possible.”
Before implementing GSDCost, VT Garment faced significant challenges due to the absence of a scientifically based time and cost standard. This gap made it difficult to forecast costs and capacity accurately, resulting in unpredictable production and capacity management. Relying on outdated historical data from various IT systems, the company struggled with inconsistent efficiency targets, frequent defects, delayed deliveries, wasted materials, increased freight expenses, and unplanned overtime.
With GSDCost, VT Garment introduced standardised benchmarks using predefined times and motion codes, allowing cross-functional teams—such as sales, costing, planning, and manufacturing—to collaborate using a unified, scientifically grounded approach to cost analysis. This alignment fostered clearer, data-driven communication across departments.
The improvements were substantial: VT Garment saw productivity gains of 6.5% to 30%, depending on product type, and achieved a 13% boost in on-time delivery. The company also reduced overtime, air freight, machine rentals, and material waste, ultimately enhancing profit margins by more than 30%.
“GSDCost has proved a real game changer for us,” adds Chalumpon Lotharukpong, managing director of VT Garment. “Not only has it enabled us to achieve more accurate planning and a substantial productivity boost across the business, but we’ve also eliminated overtime costs—saving approximately $595 each week. Our monthly machine rental expenses have dropped by $1,160 thanks to precise requirement calculations, and with our ability to quickly deliver accurate CM quotes, we’ve seen a remarkable 30% increase in profitability along with a notable enhancement to our industry reputation. We are truly honoured to have achieved GSD Excellence Gold Certification and extend our heartfelt thanks to Coats Digital’s expert consultants, our dedicated GSD practitioners, and the entire VT Garments team for their diligence and commitment to making this achievement possible.”
Tan Demir, professional service director – APAC, Coats Digital, said: “We’re thrilled to see VT Garment achieve such outstanding results since implementing GSDCost. In today’s landscape of intense global price competition and demand for faster deliveries with diverse styles, it’s essential for fashion manufacturers to stay innovative, agile, and digitally focused to thrive. By standardising SMVs based on scientific methods, apparel companies gain a decisive edge, improving production efficiencies and enabling precise, data-driven pricing in negotiations. VT Garment’s commitment to the GSD Excellence Programme has been exemplary, and its team should be incredibly proud of what it has achieved. Their expertise with GSD methodology positions them as an industry-leading force, marking them as one of the most agile and competitive players in their field.”
Key Benefits and ROI for VT Garment Co Ltd
- Improvement in SMVs of between 6.5% – 30% depending on the core style
- Improved OTDP of 13%
- Boosted profits by over 30%
- Eliminated overtime costs – saving 595 USD per week
- Reduced machine rental costs by 1,160 USD per month
- Reduced material wastage
- Eliminated last-minute freight costs
- Seamless CM negotiations between sales and factory floor
- Fair negotiated price costings for customers
- Ability to deal with complex orders
- Fact-based stable manufacturing costs
- Achievable performance incentive programme