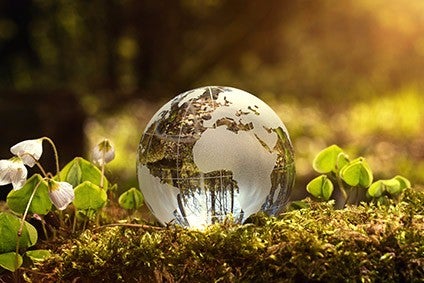
Singapore based viscose major Royal Golden Eagle (RGE) has outlined progress on its commitment to invest US$200m in next-generation textile fibre innovation and technology and revealed plans to further its work by exploring how waste can also be used as a resource.
The just-released 28-page report provides a summary of the activities undertaken by RGE’s subsidiaries involved in the fashion value chain to advance its ambition towards closed-loop, circular and climate-positive cellulosic fibre.
RGE claims to be the world’s largest viscose producer through its business groups Sateri in China and Asia Pacific Rayon (APR) in Indonesia. In October of last year, the group revealed plans to invest $200m over the next ten years into cellulosic textile fibre research and development.
The target allocation is set at 70% in scaling up proven clean technology in fibre manufacturing, 20% in bringing pilot-scale production to commercial scale, and 10% in R&D in emerging frontier solutions.
RGE has adopted a three-pronged approach to its investments: sourcing ready solutions in the market, investing in start-ups, and strengthening its in-house R&D capabilities.
In the past 12 months, notable achievements include the launch of Finex, a Recycled Claim Standard (RCS)-certified fibre containing up to 20% recycled content produced using a 35,000 tonne per annum commercial line, inaugural production of lyocell, a closed-loop fibre that uses minimal chemical and a solvent that is nearly fully recoverable and recycled, as well as new R&D facilities in China and Indonesia. It also initiated an in-house cotton textile waste recycling project.
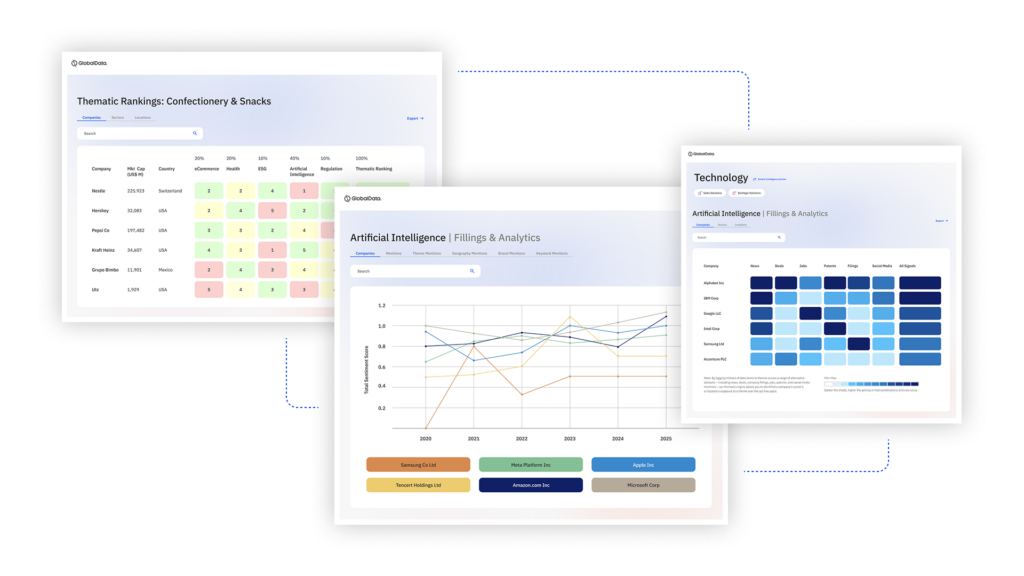
US Tariffs are shifting - will you react or anticipate?
Don’t let policy changes catch you off guard. Stay proactive with real-time data and expert analysis.
By GlobalData“We pride ourselves on the fact that the virgin resources we draw on to make a range of daily essential products are renewable. But this does not mean that we rest on our laurels. In fact, we are taking our sustainability commitment to the next level by exploring how waste can also be used as a resource to regenerate new materials and give rise to a truly circular economy,” says Bey Soo Khiang, vice chairman of RGE.
As part of these plans, Sateri is in discussion with the China Association of Circular Economy (CACE) to commission a study on the recycling and utilisation of textile waste in China. The project, which will commence in early 2021, will analyse the output, utilisation, demand, investment risks and regulatory landscape of the textile waste industry with the aim of informing the industry on strategies to unlock the potential of textile circularity in China.
The report also presents targets for RGE’s two viscose business groups for the first time.
Sateri is set to have a product with 50% recycled content by 2023, and to reach 100% by 2030. It also aims for 20% of its feedstock to contain alternative or recycled materials by 2025. APR, meanwhile, will source 20% of its feedstock from alternative or recycled materials by 2030.
In the area of closed-loop manufacturing, all existing Sateri and APR mills will meet EU-BAT emission limits by 2023.
Allen Zhang, president of Sateri, said: “I am very pleased with our progress in the past year. We have advanced quickly in spite of the challenges brought on by a global health pandemic.
“As a large and growing fibre producer known for product quality and cost-competitiveness, volume is both an advantage and disadvantage; while we are well-placed to scale solutions, we are currently constrained by the readiness of circularity-specific technology and, in the case of textile recycling and non-wood feedstock, the availability and volume of alternative feedstock. But with clear goals towards 2030, we are committed to accelerating our efforts.”
Click here for just-style’s recent interview with Zhang on why the Covid-19 pandemic has underlined the importance of a resilient and agile supply chain.