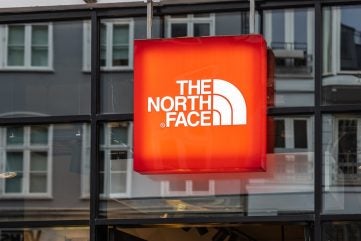
The collaboration with The North Face marks a key moment for Bottle, spearheaded by the National Renewable Energy Laboratory (NREL), as the group aims to scale PHA production for real-world applications in outdoor apparel.
Over the next year, the consortium will produce several pounds of PHA fibre, which will undergo rigorous testing and evaluation by The North Face for incorporation into its product lines.
After reviewing the initial results, The North Face plans to test prototype fibres with its suppliers to evaluate a line of more sustainable products.
“We are committed to making the best-performing products while leaving an ever-smaller footprint on the planet,” said Carol Shu, senior manager for global sustainability at The North Face.
“Materials innovation is a pinnacle of our brand, and this project not only brings to life new possibilities for synthetic textiles but also supports our focus on enabling product circularity.”
Under the leadership of polymer scientist Katrina Knauer, Bottle has been at the forefront of developing PHAs as a viable alternative to conventional polyester. Unlike their petroleum-derived counterparts, PHAs claim to offer biodegradability and compatibility with recycling processes, presenting a promising solution to the issue of textile-related microplastic pollution.
Through years of research and innovation, Bottle scientists, in collaboration with Colorado State University, have engineered PHAs with properties akin to conventional polyester, while retaining their biobased and biodegradable nature.
Beyond performance, the collaboration seeks to address the broader environmental implications of textile production. By analysing the energy and carbon intensity of PHA production and simulating microfiber shedding and biodegradation, the project aims to provide comprehensive insights into the sustainability of PHA textiles compared to traditional polyester.
Recent advancements in synthetic routes have enabled more precise control over PHA’s chemical structure, enhancing its mechanical toughness and recyclability.
“We’re actually showing we can control the microstructure to get PHA to behave like polyester fibres and textiles,” Knauer explained.
According to Ravikumar Gowda, a Bottle researcher based at Colorado State University, the material’s recyclability hinges on specific changes to PHA’s chemical backbone.
Gowda said: “Our redesigned PHA structure substantially increases mechanical toughness and renders the new PHA chemically recyclable to its building-block monomer with a simple catalyst and heat.
“The recovered monomer can be reused to reproduce the same PHA again, in principle, infinitely.”
In February, the technology platform for branded resale Archive joined forces with Advanced Clothing Solutions (ACS), a UK circular and sustainable fashion fulfilment hub to offer cleaning, repair, and second-hand item fulfilment on a branded resale market with global brands The North Face and Pangaia already leveraging this partnership.