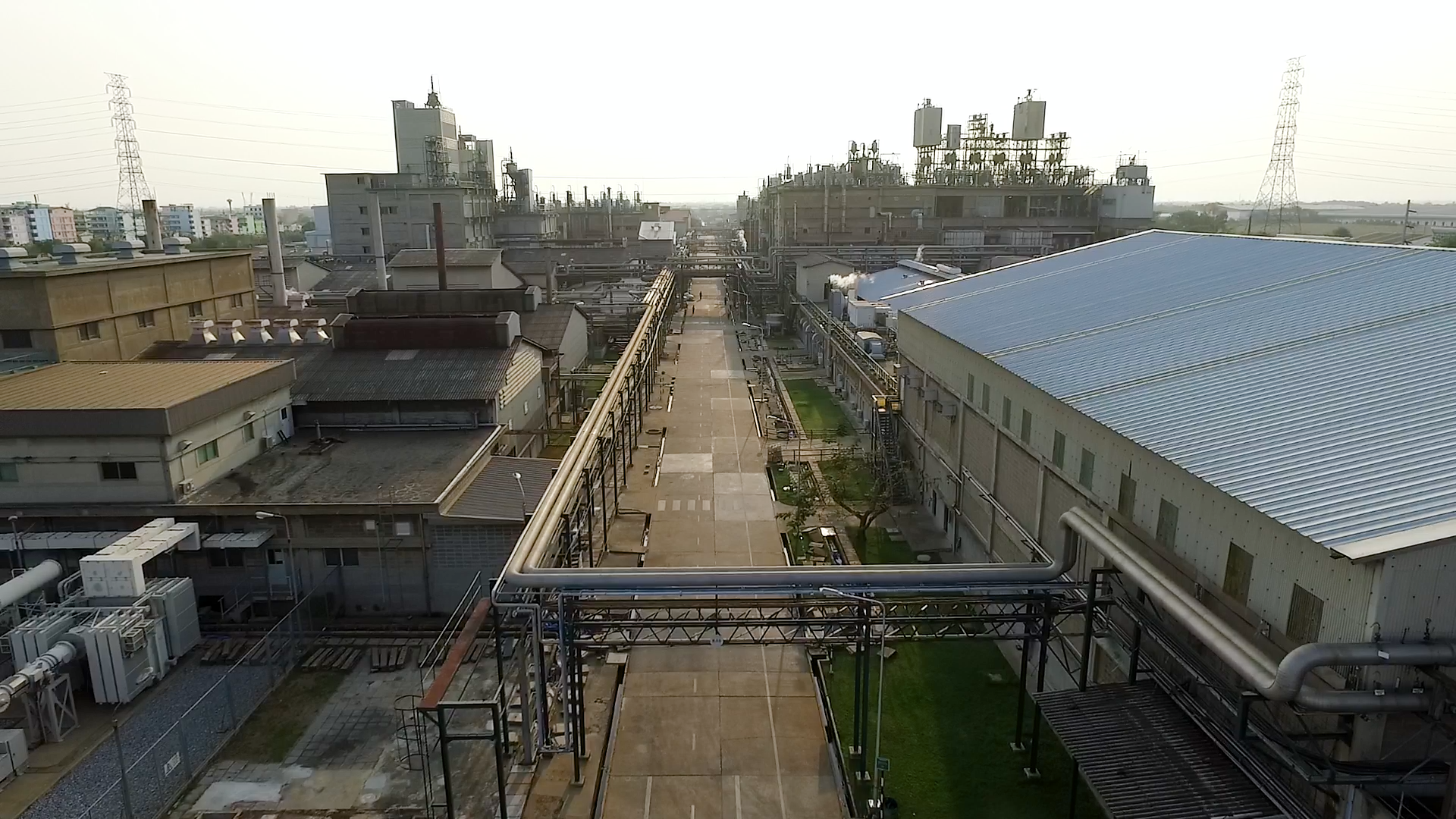
Teijin Polyester (Thailand) Limited said operations on the new facility began this month. The facility is equipped with multi-spindle spinning machines for polyester multifilament yarn and machines capable of adding functional agents.
Teijin Frontier invested approximately JPY1bn (US$6.8m) to construct the facility, which is expected to produce 1,500 tons of polyester filaments annually by the fiscal year ending in March 2024.
The facility will enhance the added value of Teijin Polyester (Thailand) Limited including through extra-efficient spinning and an automated process for the uniform drying of multifilament. The company will effectively use the new facility to produce Teijin Frontier’s proprietary polyester filaments for apparel and interior applications, such as the Octa highly modified hollow-core fibre and a water-absorbing quick-drying yarn.
Teijin Frontier expects to expand the range and improve the functionality of its EcoPet recycled polyester fibres by integrating the new facility with a separate facility that started operating at Teijin Polyester (Thailand) Limited in January to convert used plastic bottle flakes sourced in the Thai market into recycled polyester chips.
The new facility accommodates various special polymers and recycled raw materials and additionally can add functional agents to raw yarn for the production of new types of functional polyester filaments.
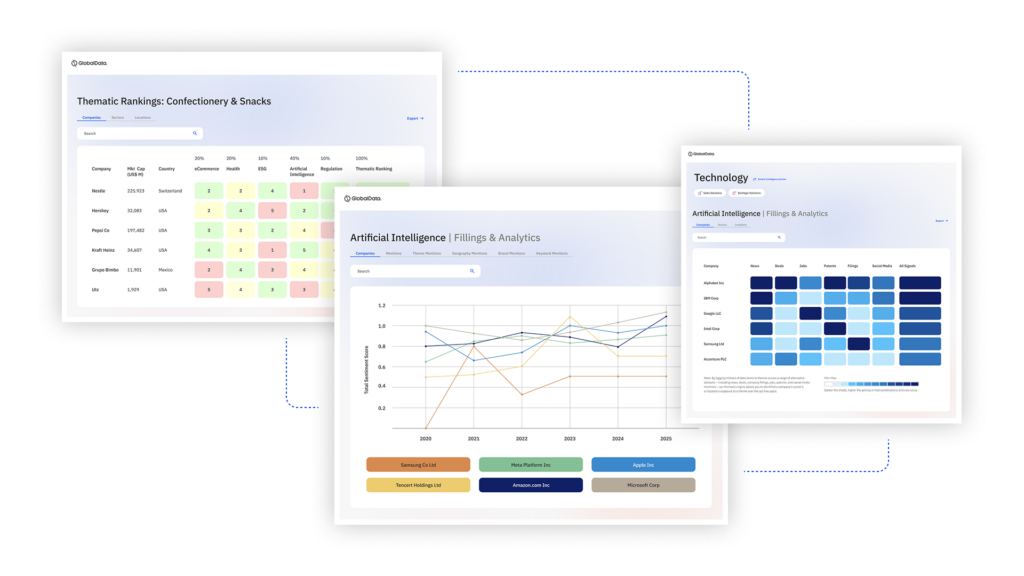
US Tariffs are shifting - will you react or anticipate?
Don’t let policy changes catch you off guard. Stay proactive with real-time data and expert analysis.
By GlobalData