US denim company Silver Jeans Co has managed to double its number of product lines, reduced product lead time by 10%, and lowered sample lead times after successfully implementing a new PLM system.
Founded in 1991 by Michael Silver as an extension of Western Glove Works, today Silver Jeans Co has six offices across Canada and the US as well as a factory centre in Hong Kong and sells through distributors in Europe, Japan and Australia.
The business operates on a four-season basis and develops 100-200 SKUs per season across its six lines: Men, Big and Tall, Women, Plus, Sportswear and Maternity.
“With multiple people handling data, there was no direction and ownership wasn’t clear when something needed to be addressed,” explains Robyn McCarthy, global merchandising manager at Silver Jeans Co. “We wanted to increase the number of products but had no clear way of managing that process. It became obvious that we needed a programme that would help us to achieve our company goals.”
Since implementing Centric PLM, Silver Jeans Co has doubled its number of product lines since 2010, reduced product lead time by 10%, lowered sample lead times by an impressive 25% and reporting that used to takes days, can be completed in minutes, the company says.
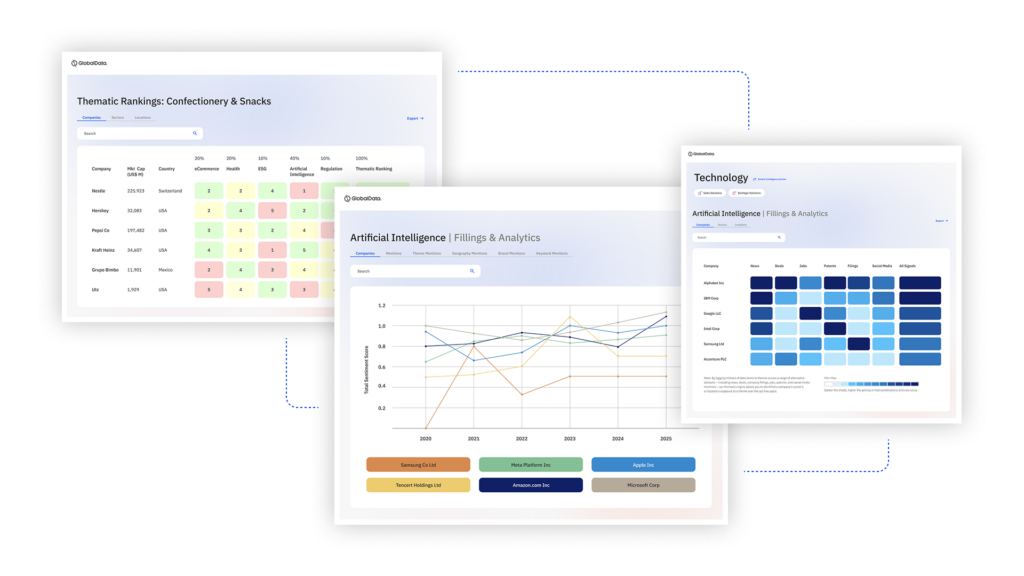
US Tariffs are shifting - will you react or anticipate?
Don’t let policy changes catch you off guard. Stay proactive with real-time data and expert analysis.
By GlobalData