
Lenzing says its new resource-efficient dyeing approach significantly reduces environmental impact and is ideal to use on pre-treated fabrics and yarns made with Tencel Lyocell fibres.
The new dyeing approach covers a yarn pre-treatment and knitting technique to achieve aesthetics that resemble the wash-down effects of traditional dyeing in ready-to-wear and knit garments.
As part of the process, Lenzing highlights that only one round of dyeing is required, leading to a reduction in water, energy and chemical usage by up to 50%, 40% and 90%, respectively.
Additionally, with the new approach’s direct application to Tencel Lyocell fibres or Tencel Lyocell with Refibra technology, different shades of colour, wash-down or fade-out effects can be customised.
The company says this makes it ideal to produce ready-to-wear, knit apparel and denim-looking garments in various colour shades.
“As consumers become more conscious of the environmental footprint of their purchases, designers and manufacturers are seeking innovative ways to ensure that the materials and production processes deployed have a low environmental impact, while expanding design possibilities,” says Rex Mok, vice president of fibre technical marketing and development at Lenzing.
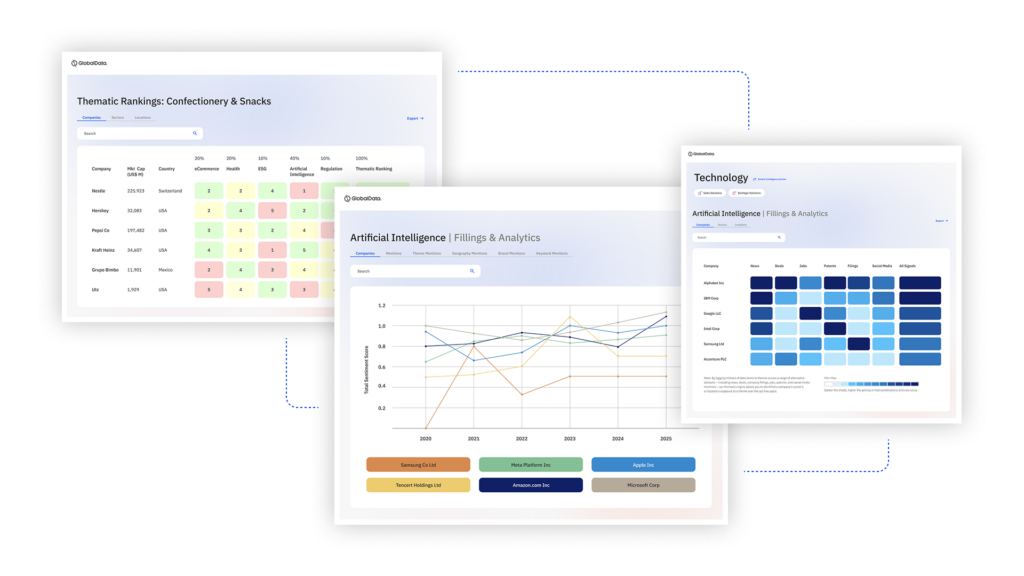
US Tariffs are shifting - will you react or anticipate?
Don’t let policy changes catch you off guard. Stay proactive with real-time data and expert analysis.
By GlobalDataMok continues: “Our new approach can create wash-down aesthetics or vintage looks on any knit fabric without water-intensive bleaching processes. By overcoming the limitations of traditional dyeing, our new approach is a resource-efficient alternative that helps translate into greater sustainability and more competitive operational costs for fabric mills. We will continue to work with mill partners to drive wider adoption of the new approach and explore new applications within the textile value chain.”
In fact, Lenzing adds the approach is in line with the wet-processing and production facilities of fabric mills which can bring additional benefits for value chain partners.
The company points out no residue is left behind as part of the process, which minimises machine downtime when changing colour lots, and production delays are also shortened so yarn makers and fabric mills can save costs while enhancing production efficiency and sustainability.