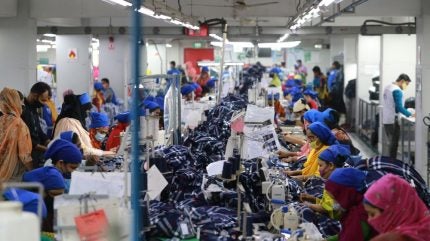
As part of its online Purchasing Practices: Who Pays For The Crisis, tracker the Business & Human Rights Resources Centre (BHRRC) updated its monitoring of the purchasing practice brand allegations at factories across apparel-producing countries.
BHRRC reported that multiple apparel brands stated past contract terminations as justification for limited responses to the direct responsibility allegation, even though they were contacted specifically to explain the reasoning behind divestment and how these decisions were linked to purchasing practices and their impact on labour rights.
This information was collected by the organisation by contacting 57 fashion brands, with a response rate of 53%, to find out which brands’ purchasing practices have been linked to labour rights abuses in the global factories.
Nearly half (46%) of fashion brands distanced themselves from direct responsibility for the labour issues BHRRC raised by highlighting that the incidents either occurred outside of their own facilities or happened after the brand had ceased operations with the factories involved.
While some of the brands claimed robust engagement with trade unions, only 10% of brand responses show substantial direct interaction with workers or their representatives in addressing allegations.
Seven fashion brands mentioned having some form of a remediation mechanism to deal with allegations brought to them but only three brands outlined how they were put into practice to deal with the specific allegations raised.
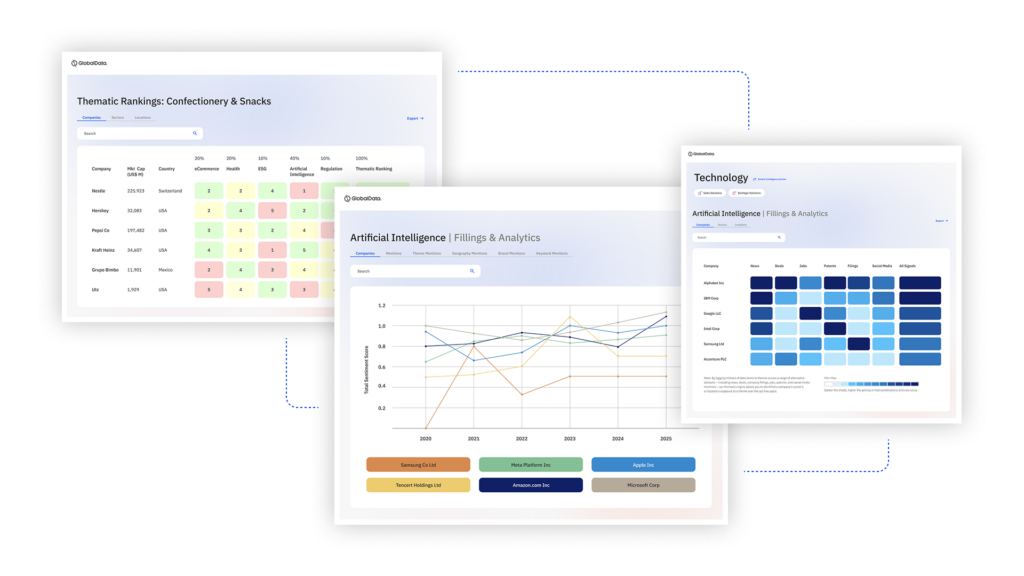
US Tariffs are shifting - will you react or anticipate?
Don’t let policy changes catch you off guard. Stay proactive with real-time data and expert analysis.
By GlobalDataBHRRC said 11 brands reported relying on local law to help remedy the allegations raised. It advised these companies to “move beyond” these local regulations, which they are say are often often “inadequate” and may not always align with good practice labour standards.
Brands’ supply chain woes
According to BHRRC, the fashion industry continues to grapple with myriad global economic challenges, including inflation, geopolitical conflicts, and energy crises. This has led to decreased demand and significant shifts in purchasing practices, with over a third of suppliers globally facing up to 10% order cancellations in just four months, resulting in unpaid wages and mass layoffs.
In 2022, the centre found that 75% of the UK’s food bank clients in Leicester were garment workers.
In the first five months of 2023, Vietnam saw 70,000 job losses with 17,000 workers let go without compensation. Pakistan saw 700,000 job losses between 2022 to mid-2023 with up to 30% factory closures in the region around the same time.
Yet despite this, the industry managed to maintain substantial profitability, driven by luxury and a small group of the top 20 most profitable brands, which contributed to 99% of the industry’s profits.
BHRRC monitored an increase in technological changes ranging from the shop floor to the supply chain as brands double down on cost efficiencies, renegotiation sourcing agreements and two-thirds consider nearshoring.
These strategies are not impact neutral: they affect suppliers and in turn, workers leading to workforce cuts, unpredictability of orders affecting workforce planning, delayed orders, deferred payments, and demands for lower prices from suppliers.
“Suppliers are being compelled to accept lower prices since retailers will not continue placing orders with them if they don’t agree to the new prices,” said Mohammad Hatem, executive president of the Bangladesh Knitwear Manufacturers and Exporters Association. “Sometimes, the prices are lower than the production cost.”