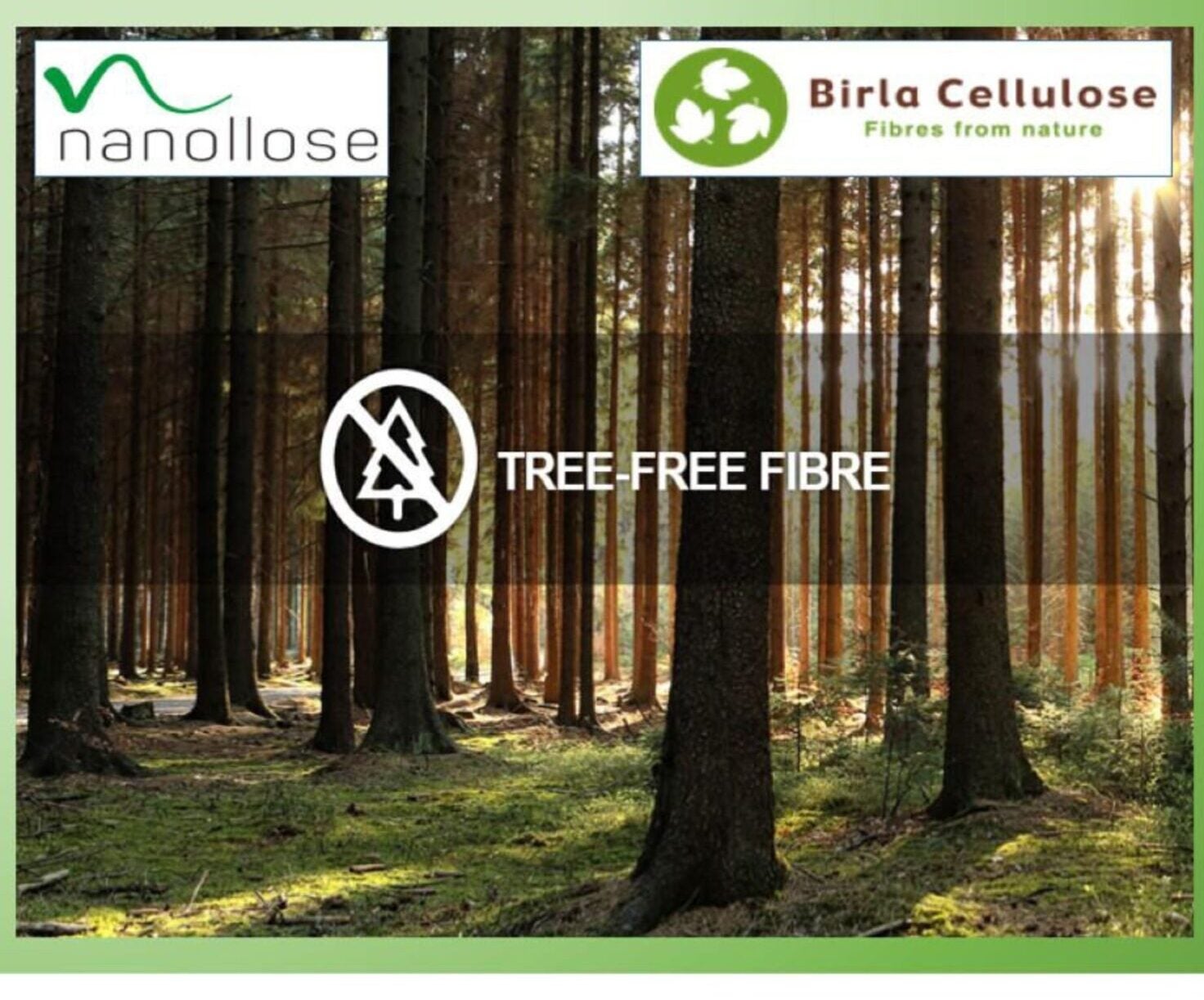
The company says the first pilot spin to produce 250kg of this fibre marks a significant milestone in Birla Cellulose’s strategy for commercialisation of the technology which uses sustainable biomass produced from the fermentation of food industry waste.
Chief technology officer of the Aditya Birla Group and Birla Cellulose, Dr Aspi Patel, said: “Developing state-of-the-art technology for industrial-scale lyocell production, using tree-free cellulose, is an exciting development in the area of next-generation alternative feedstock. We are looking forward to scaling up this technology in collaboration with Nanollose.”
The company says that all the fibres produced maintained all superior attributes of Birla Excel (lyocell) such as comfort, strength, durability and moisture absorption while further enhancing the sustainability quotient by using Nanollose’s microbial cellulose, reducing pressure on virgin wood-based pulp.
Australian-based biomaterial technology company Nanollose Ltd is the creator of eco-friendly tree-free rayon fibre, Nullarbor, sourced from sustainable coconut waste.
Executive chairman of Nanollose, Dr Wayne Best, said: “The completion of our first pilot spin is a significant milestone in the Company’s development and provides clear proof of concept of our offering at scale. This milestone provides Nanollose with a strong growth foundation for the next 12 months.”
The target is to increase the scale and/or percentage of microbial cellulose in subsequent pilot spins and allow Birla Cellulose to produce quantities of several Nullarbor fibres consisting of varied percentages of microbial cellulose, mixed with other cellulosic materials.
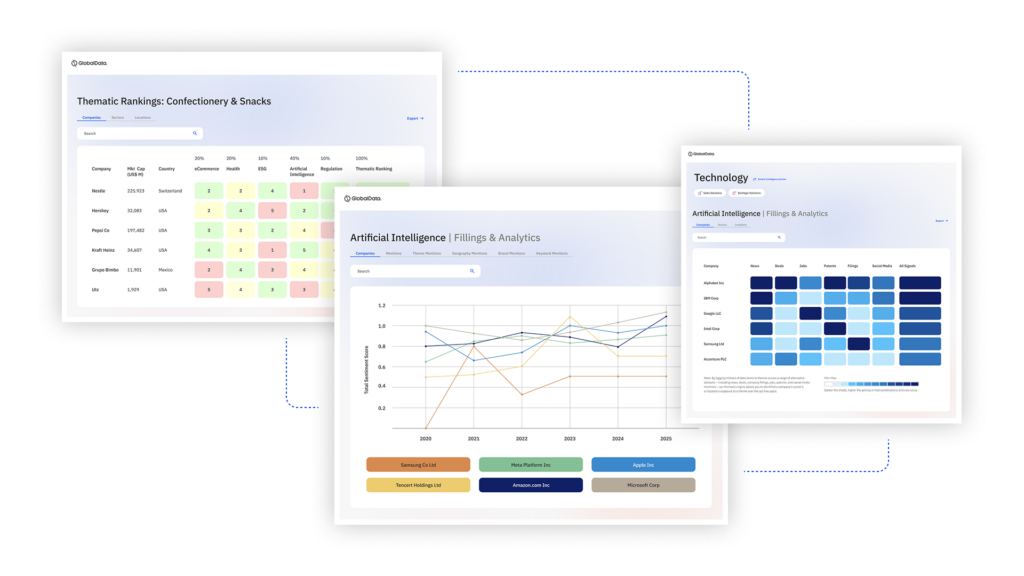
US Tariffs are shifting - will you react or anticipate?
Don’t let policy changes catch you off guard. Stay proactive with real-time data and expert analysis.
By GlobalDataCompletion of the first pilot-scale spin process follows months of extensive work, the company said, and highlights the capabilities of Birla Cellulose’s and Nanollose’s technical teams to overcome the challenges associated with scaling production from laboratory to industrial-grade processing across multiple continents.
Birla Cellulose’s fibres are made from renewable wood and are produced using a closed-loop process, to significantly lower carbon emissions and resource consumption. Its eco enhanced fibres such as Livaeco viscose and modal, Birla Excel (lyocell), and Birla Spunshades are designed with superior sustainable credentials, the company says.
Birla Cellulose says it works closely with global sustainability focussed organisations like Sustainable Apparel Coalition (SAC), Canopy, Zero Discharge of Hazardous Chemicals (ZDHC), Changing Markets Foundation, Textile Exchange, WBSCD, Fashion for Good, Global Fashion Agenda, The Microfibres Consortium amongst others to continually learn and apply the best practices in its global operations and across its value chain.