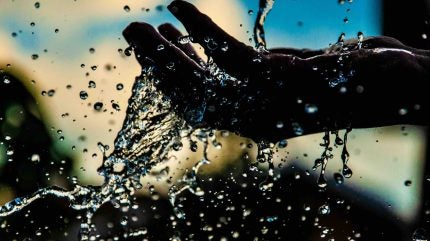
By transitioning to OEKO-TEX-approved water-based inks, AAG aims to mitigate health risks for its workforce, local communities, and consumers alike as traditional apparel manufacturing tends to rely on inks with harmful chemicals such as phthalates, petroleum-based co-solvents, and PVC.
CEO of Active Apparel Group, Daniel Hawker, emphasised the significance of this initiative, stating: “Reducing toxic chemicals from the manufacturing process is the right thing to do for our employees, for people living close to our manufacturing facilities, and for anyone buying the apparel that we manufacture.”
OEKO-TEX 100 Class 1 Standard Printing Inks represent a specialised category of inks known for their compliance with stringent certification standards. These inks are said to guarantee the absence of harmful substances, making them safe even for the most sensitive skin.
In addition to safeguarding human health, they claim to offer significant environmental benefits by reducing the risk of allergens and harmful chemicals leaching into the environment.
Hawker further explained: “Moving away from toxins also allows us to keep ahead of increasingly stringent environmental regulations, allowing our customers to stay profitable in a quickly changing global marketplace.”
AAG’s commitment to sustainability extends across its range of printing methods, including digital printing, screen printing, and heat transfers for on-garment logos and care instructions.
While OEKO-TEX-certified water-based inks are used predominantly for digital printing, they are increasingly integrated into screen printing processes as well, offering a socially and environmentally better alternative to conventional Plastisol inks.
AAG said it is making a “sizeable environmental impact” with its printing operations. Its digital printing averages 25,000 meters per month and screen printing reaches 60,000 garments per month.
However, the company highlights that the transition to water-based inks requires a skilled production team, and AAG is actively investing in ongoing training for its 30 employees at its printing operations in Ningbo, China.