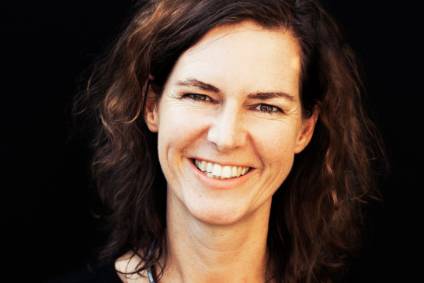
An overhaul of the auditing process on factory safety and working conditions is long overdue – and a new initiative launched this month could offer the solution. The Social & Labour Convergence Program’s Converged Assessment Framework enables apparel brands and retailers to leverage one set of verified social and labour data, reduce the amount of money spent on duplicated auditing, and instead free up resources to improve efficiency and factory working conditions. SLCP executive director Janet Mensink, and Peter Higgins, senior director of global responsible sourcing at VF Corp, tell just-style more.
Audits are one of the most commonly used methods to assess factory safety and working conditions. Yet they also come with a heap of complexities where the apparel industry is concerned. To start, one factory may produce for several brands, each with its own audit requirements, and spend the greater part of a year dealing with auditors to ensure compliance.
Because there is no single source of audit data – or standardisation – in the apparel, textile and footwear industry, brands and retailers have also ended up with conflicting requirements. Not only does this lead to a huge amount of extra but non-value-added work, but it also reduces transparency and leaves the industry vulnerable to increased scrutiny from governments and the media.
In addition, as the speed of fashion consumption accelerates, clothing and footwear brands are faced with producing more, faster. At the same time, there is pressure to ensure this is done in a way that is not at the expense of worker health and safety, and also considers the impact on the planet. For some brands, whose supply chains span across several geographies, that can be a huge challenge to manage, adding to both time and cost.
The pressure to respond to multiple audits has led to the global industry calling for a way around the problem. The goal is to find a way to enable firms to share data and reduce the number of audits carried out across the supply chain, and eliminate so-called “audit fatigue.”
It is an idea the industry has been thinking about for several years. Back in 2012, the Global Apparel, Footwear and Textile Initiative (GAFTI) was proposing the idea; bringing together retailers, brands, mills and factories to try and reduce the complexity of compliance. At the time it was received as “sounding great…but a little futuristic” by some brands.
How well do you really know your competitors?
Access the most comprehensive Company Profiles on the market, powered by GlobalData. Save hours of research. Gain competitive edge.
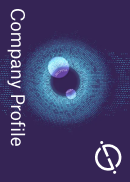
Thank you!
Your download email will arrive shortly
Not ready to buy yet? Download a free sample
We are confident about the unique quality of our Company Profiles. However, we want you to make the most beneficial decision for your business, so we offer a free sample that you can download by submitting the below form
By GlobalDataBut calls for a unified approach to measurement haven’t receded.
The need for a single audit approach
“Manufacturers are being confronted with another audit almost every week that is 95% the same as the last and they’re spending so much time and money doing the same thing over and over again”
“Everyone acknowledged all the good things about social compliance, the need for it, as well as all the risks associated with supply chains,” explains Janet Mensink, the executive director of the Social & Labour Convergence Program (SLCP).
“Brands basically wanted to manage that but came up with their own systems. This drove so many duplications. In the end, manufacturers are being confronted with another audit almost every week that is 95% the same as the last and they’re spending so much time and money doing the same thing over and over again.”
The SLCP launched at the end of 2015 with the aim of improving labour conditions in global supply chains through the creation of sustainable remediation.
Earlier this month the body announced the launch of its Converged Assessment Framework (CAF), a tool designed to eliminate audit fatigue by replacing current proprietary tools with a single framework for social and labour compliance in the apparel and footwear industry.
It is the result of three years of work between the SLCP’s 200 signatory brands – including Nike and VF Corp – retailers, industry groups, international and governmental organisations, service providers and civil society groups.
Mensink says the aim of any audit is to improve labour conditions and processes. One uniform set of verified data that can be used by everyone allows the unlocking of resources that can be used more wisely, for example in remediation or capacity building or spend “in the things that really matter.”
But one of the biggest challenges of developing a single tool is that it needs to fit an industry which is composed of so many different stakeholders. For example, beyond brands and manufacturers, there are NGOs, investors, and even consumers, who are increasingly demanding greater transparency from the clothing and footwear brands that serve them.
“There were some really hard conversations and there were points we wondered if we’d ever get there at all”
“We had to have all the parties at the table, from brands to NGOs. But that also means that within one group, you have differences in opinion on what the most important or priority topics are. With multiple parties you get different perspectives on the same issue. At times they are polarised views and you need to find some way to reach consensus. There were some really hard conversations and there were points we wondered if we’d ever get there at all.”
Research from the SLCP in 2018 showed that adoption of the Converged Assessment Framework could unlock resources worth over US$1.5m spent on duplicative audits in 2019 alone – rising to $130m by 2023 – for re-deployment to improve working conditions at garment manufacturing facilities worldwide.
“Everyone can win with this,” asserts Mensink. “To reach a solution, we had to ask the question ‘can we live with it?’ and apply that question to a number of propositions and amendments.”
The development of the CAF
The project started with a comparison of 21 existing audit tools and revealed between 90-95% duplication across them. The plan was to produce a tool that could work across a variety of pre-existing systems without requiring any special adaptations; an agnostic framework, rather than a whole new audit system, with the idea being that everyone uses and is assessed against a single set of data.
While the first prototype was fairly straightforward to build, given it was based on questions that were common across the majority of the audit tools, the second stage proved more challenging, as it compared what one brand carried in its current audits against another that did not, for example.
Three prototypes, public consultations and two pilot tests later, a final draft of the CAF was produced, which was submitted to signatories for a vote at the end 2018 and was implemented in a ‘Light Operation’ from November 2018 to February 2019.
“Efficiency is definitely one of the drivers. But it’s not efficiency in isolation. It’s efficiency with a bigger goal to redirect those resources with a focus on remediation, for example, or transparency, or buying practices.”
“97% of them said yes, we can live with this. Go ahead, we want this to work. Efficiency is definitely one of the drivers,” says Mensink. “But it’s not efficiency in isolation. It’s efficiency with a bigger goal to redirect those resources with a focus on remediation, for example, or transparency, or buying practices.”
But auditing is big business in the clothing and footwear sector. So how have specialist audit firms reacted to the tool?
Mensink says she has seen, particularly among the more progressive auditing firms, a desire to move away from auditing in its current format, to a more monitoring or compliance-led role. Currently, 60 audit firms are signed up as signatories to the SLCP.
“Being at the table with the SLCP means that they are at the forefront of [the shift]. If SLCP succeeds and we’re able to get that efficiency and unlock resources for other value-added programmes, they can move into that. For example, the staff at an audit firm can become an approved verifier for the SLCP.
“In the short term they are driven by the benefit of being part of the SLCP but there’s the added benefit, for the more progressive firms, that want to move into the markets beyond just auditing.”
The future for CAF
After the ‘Light Operation’ the CAF (Converged Assessment Framework) is heading towards scale in four countries this month: India, China, Sri Lanka and Taiwan and additional countries later this year. They have partly been selected as priority markets for the framework because they are among the biggest producers of clothing. But launching in these markets also allows the SLCP to expose the framework to several very different environments: geographical spread, different languages, factory sizes, and logistical demands. It also gives the SLCP an understanding of the tool’s effectiveness in markets that have various conditions and risks.
And for the first time, it will provide across-the-board access to the same set of comparable social labour and data – enabling comparisons within a business but also within country by country, or sector or sub-sector.
The 2020 launch markets will include Bangladesh and Vietnam. Speaking of scaling the project, Mensink says while some of the learnings from the first four countries are transferrable, there will be challenges entering new markets, including providing training specific to that market and capacity for translation. But that is something the International Trade Centre (ITC) – the SLCP’s partner – is helping with.
The implementation of CAF has seen the Social & Labour Convergence Project graduate to become the Social & Labour Convergence Program. However, it is still at the early stages of the journey.
“2019 is still very much for us a start-up phase, and I’m sure that the CAF needs to be refined in some ways. We hope to achieve this by starting in a spread of countries. We will then work to see what issues need addressing and what is needed most from both the brand side and the stakeholder’s side.”
VF Corp, the company behind brands including Vans, The North Face and Timberland, is one of the active signatories in the SLCP and was on the steering committee from the start of the project. This year the company is targeting around 50 to 70 facilities where the Converged Assessment Framework will be applied, up from the light operations phase last year which saw 14 factories participate. Here, Peter Higgins, senior director of global responsible sourcing at VF Corp, tells just-style about the CAF and how it can benefit brands.
What did you find were the biggest issues surrounding audits?
“If you look at the industry, one of the biggest issues that we have is factories with multiple customers will have a significant amount of redundant audits. So each brand is performing its own audits and it’s leading to a pretty inefficient process. We have some factories that have up to 30 audits in a year that could take anywhere between one to five days. The SLCP is a great opportunity for us to leverage one common assessment, thus freeing up resources to reinvest in improving working conditions in factories for workers, for the environment.
Has the adoption of the CAF proved challenging in any way?
Any time you’re trying to implement a new process into a machine – we conduct more than 2000 audits a year – it’s certainly challenging. I know many other companies are facing that, just given the breadth and scale of our supply chains. But from a tool perspective, from the questions being asked, from the process and from the organisation itself, things are running quite smoothly for the first 1-2 years of a new programme.
What are the biggest business benefits of adopting the new CAF?
I don’t see this – and certainly VF doesn’t – as an opportunity to increase profit margins. This is an opportunity for us to gain efficiencies that can be reinvested in workers and working conditions. So we’re not approaching this from a cost savings perspective but more as an opportunity to enhance our existing programmes around responsible sourcing.
How about the industry benefits?
The broad umbrella of organisations who are supporting the SLCP from the industry, but also from different labour groups, government organisations, and NGOs allows us to get smarter and to get better. If we’re developing a tool with many different brains at the table – both from industry and outside of industry – that tool would be a much better tool than if a brand develops it on its own. We’ll have a smarter and more efficient assessment tool and process to allow us to get to our goals and improve working conditions in factories around the world.