With around 20% of the world’s cotton coming out of the Xinjiang region of China, a new report argues laws aimed at eliminating inputs from the region can only be effective if new sourcing hubs are developed and the capacity to trace products back to their source is significantly strengthened.
China’s Xinjiang Uyghur Autonomous Region (XUAR) produces around one-fifth of the world’s cotton and is the country’s largest exporter of textiles and apparel. Much of this raw cotton is also spun into yarns that are used in factories globally.
But due to repressive government programmes transferring hundreds of thousands of Muslim Uyghurs and other ethnic and religious minority groups in Xinjiang, production in China may introduce forced labour into global supply chains.
To avoid these forced labour-affected inputs, multiple actors must work together to develop new sourcing opportunities, according to a new report from the CSIS Human Rights Initiative, which has identified strategies for businesses, governments, NGOs, and multilateral organisations to tackle forced labour linked to the XUAR.
‘Addressing Forced Labor in the Xinjiang Uyghur Autonomous Region: Collective Action to Develop New Sourcing Opportunities’ argues that to speed the development of alternative sourcing hubs that are free from XUAR-linked forced labour, there must be a coordinated effort to encourage long-term investment in new locations. International human rights and environmental standards must also form a fundamental element of the strategy, it says.
Industry experts have suggested the development of new sourcing hubs typically takes around ten years.
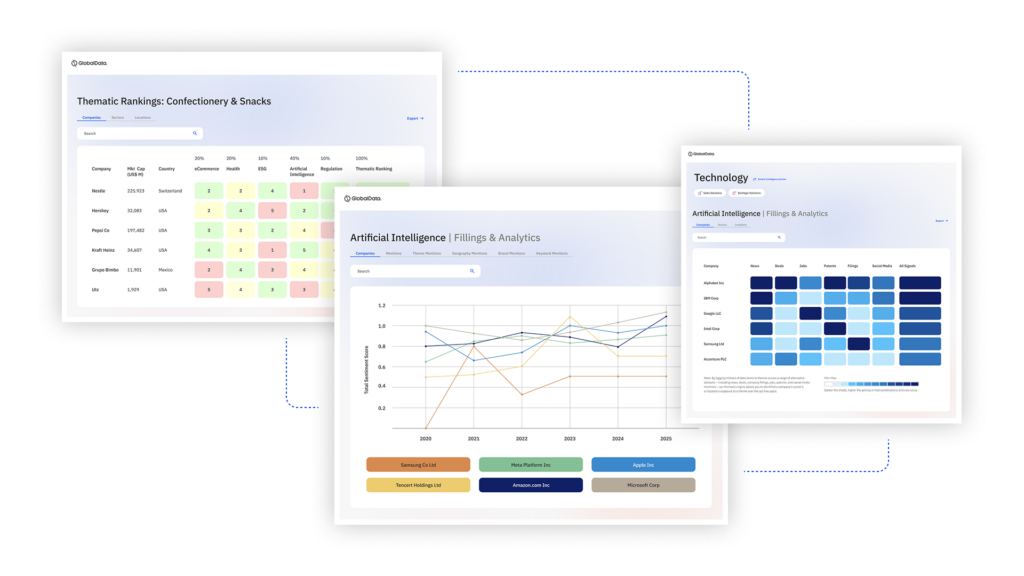
US Tariffs are shifting - will you react or anticipate?
Don’t let policy changes catch you off guard. Stay proactive with real-time data and expert analysis.
By GlobalDataNew sourcing hubs for textiles, apparel, and footwear must be vertically integrated as much as possible within the region or country, both to avoid XUAR inputs and create cost efficiencies
“New sourcing hubs for textiles, apparel, and footwear must be vertically integrated as much as possible within the region or country, both to avoid XUAR inputs and create cost efficiencies,” reads the report.
“This requires substantial investment in yarn and textile mills, which require expensive equipment and skilled workers and do not provide a return on investment for a number of years.
“To grow or establish new hubs, a country or region must provide appropriate incentives, such as adequate infrastructure, ample investment, openness to labour rights and environmental protections, and opportunities for worker upskilling.” The research also calls for tariffs and trade arrangements that encourage the development of country or regional hubs, as well as development assistance to improve the supporting infrastructure.
Such diversification brings a number of benefits beyond eliminating XUAR-linked forced labour, it suggests, including greater flexibility and resilience to supply chain shocks – a growing priority in the Covid-19 era. It can also support reshoring and nearshoring.
Implemented thoughtfully, diversification could also assist with the UN Sustainable Development Goals by providing decent work and integrating stronger environmental standards.
China as a major sourcing hub
China plays a vital role in almost all aspects of the value chain, including cotton farming, yarn spinning, textile and fabric manufacturing, and garment cut-and-sew. In addition to its own production, China exports yarn, fabric and garments to neighbouring countries such as Bangladesh, Vietnam, Cambodia and Indonesia.
China has established itself as a dominant player due to its combination of scale, diversity, technical capacity, and vertical integration. In 2019, it exported four times as much as Bangladesh, the second-largest exporter, by dollar value. Further upstream in the supply chain, the value of China’s textile exports is almost seven times the value of exports from the next largest textile manufacturer.
Long-term trends will accelerate the movement of cut-and-sew facilities out of China, and as the country continues to transition toward high-technology and skill-intensive industries, the relative importance of the apparel industry is likely to decrease. Finally, global macroeconomic trends predict higher labour costs and a shrinking workforce in China.
The likely candidates
Asian countries outside of China are the most likely to be able to quickly scale up their production of yarn and textiles and provide an alternative, mostly vertically integrated, sourcing opportunities. Several already produce yarn and textiles, albeit in limited volumes.
Manufacturers in this region often have the ability to offer more technical products, including not only textiles but athletic footwear that require sophisticated equipment. Apparel companies are often familiar with the region and may have strong relationships with suppliers based in South and Southeast Asia. However, sourcing from the region presents potential challenges, especially if the goal is to eliminate inputs linked to XUAR forced labour from the supply chain.
East Asia has no cotton, although it is unlikely to import much cotton from China at the moment since China uses its cotton internally. These countries are likely, however, to turn to China for yarn and textiles unless and until their own capacity to produce these materials is scaled up. If companies engage with their suppliers regarding avoiding XUAR-linked inputs and develop the ability to test these products’ origins using modern technologies, this concern could be addressed.
Vietnam
In the near-term, it is likely that Vietnamese yarn, textile, and footwear production will be one of the biggest beneficiaries if brands try to reduce their dependence on China. However, for the moment, Vietnam is heavily reliant on Chinese imports. In particular, Vietnam relies on China for about 60% of fabric, 55% of yarn and fibre, and 45% of trims used in apparel production. Domestic yarn and textile production has increased in Vietnam, and it sources much of its cotton from the United States. But significant investment in the Vietnamese textile industry is needed to reduce Vietnam’s reliance on Chinese imports, and Vietnam would need a reliable source of cotton as well.
Bangladesh
If brands begin to move away from sourcing in China due to concerns about links to XUAR forced labour, Bangladesh may also become increasingly vertically integrated. There is already some interest in vertical integration, and textile mills are starting to develop. Bangladesh imports increasing amounts of cotton from West Africa due to quality concerns with cotton from India; in 2018 and 2019, 41% of imported cotton was from Africa. Despite health and safety gains in Bangladesh, substantial improvement is needed, particularly regarding freedom of association. In 2019, workers faced mass dismissals and arrests in response to labour disputes and collective action, amounting to the largest crackdown on workers in years. Most recently, garment workers have reportedly gone unpaid during the Covid-19 pandemic, and labour compliance remains a significant concern for apparel companies.
India
India is the world’s largest cotton producer and has further capacity for increasing production. Similar to West Africa, production of cotton in India is characterised by low yield rates and mostly smallholder farms. However, the inconsistent quality of cotton presents challenges for India’s attractiveness as a major vertically integrated sourcing destination. Still, the country is the world’s second-largest textile exporter, and the national government has invested in the textile industry, recently setting up a national textile plan to upgrade technology, improve productivity, and promote textile exports. Labour rights vary across India’s geographic regions, with significant challenges related to child and bonded labour, including in agriculture. Labour rights have been eroded under the Modi government, including several states suspending labour laws during the Covid-19 crisis.
Indonesia
Exports from the textile and garment industry grew by one-third from 2018 to 2019, although the industry remains 40% the size of Vietnam’s. But as part of its Industry 4.0 masterplan unveiled last year, Jakarta announced plans to relax foreign investment restrictions to encourage capital inflows. Impediments remain, including exceptionally high logistics costs compared to its regional neighbours such as Malaysia and Thailand. Electricity and gas prices are also high compared to other textile producing countries, while labour costs have increased annually.
Pakistan
Pakistan’s reputation has limited buyers’ willingness to engage with producers. Domestic producers must often work through intermediaries or meet in nearby countries. Yet individuals who have had firsthand experience with Pakistan’s garment exporting industry remark that factories are better run than those in nearby countries and that infrastructure has improved dramatically. Because foreign companies are often located in designated economic zones, targeted government policies to attract FDI and improve security could help Pakistan increase exports in existing product categories. However, this will require a sustained commitment to the industry within a long-term vision for success as well as an improved security environment.
Reshoring and nearshoring
In the aftermath of the Covid-19 pandemic, US manufacturing firms have begun to rethink supply chains, and many have expressed interest in reshoring and nearshoring. With automation and capital investments in textile production, nearshoring may also present a cost-effective alternative. Investment in the textile and apparel industries of Latin America could bring long-term economic stability to the region.
However, the technical abilities of many manufacturers in the region are limited, meaning that it may only be able to produce relatively simply apparel. For the European market, Turkey is the most likely candidate for nearshoring. It can produce a wide variety of yarn and textiles.
United States
Currently, the United States is the third-largest producer of cotton in the world, after India and China. Several initiatives have focused on strengthening the textile industry in the United States, with a focus on technical fibres and textiles, where the cost of labour is a less decisive factor. In recent years, reshoring has taken place at a modest pace. Because of high labour costs associated with manufacturing apparel in the United States, it is likely that US textiles would be exported to countries in Central America for final apparel production. Along with strategies related to government procurement, it may be worthwhile to focus on efforts to increase yarn and textile production within the United States, which can promote nearshoring and regional integration within North and Central America.
Mexico
Assuming that fabric costs were the same, estimated price comparison for a pair of jeans revealed that production in Mexico would be 12% cheaper than production in China, with significantly faster time to market.
In the future, growth may accelerate as a result of the US-Mexico-Canada Agreement (USMCA), and Mexico is a likely candidate for nearshoring. Because of USMCA rules of origin, it is likely that a significant portion of Mexico’s exported apparel would consist of American-made yarn and textiles. Due to transport and duty savings, nearshore options may be cheaper than production in China or other Asian countries. Assuming that fabric costs were the same, estimated price comparison for a pair of jeans revealed that production in Mexico would be 12% cheaper than production in China, with significantly faster time to market.
Central America
Countries in Central America typically produce relatively simple items that do not require substantial technical capacity. Factories in these countries also manufacture casual shoes that require fewer parts that are not as technical and need less tooling. Thoughtful US investment in the region could assist with supply chain diversification while helping to build stronger economies and opportunities that would complement other US efforts to stabilise and improve the region’s economy and human rights conditions.
Turkey
Turkey is a substantial textile supplier, exporting more than $11bn worth of textiles in 2019. Turkey is much less dependent upon China for early inputs in the supply chain, importing cotton from a variety of countries, with the United States making up the largest share. Cotton yarn is primarily imported from Turkmenistan and Uzbekistan, both of which have faced significant problems with state-sponsored forced labour in their cotton fields. This could become less problematic if Uzbekistan continues on its current positive trajectory on forced labour, and Turkish textile producers are simultaneously pressured to stop sourcing from Turkmenistan. Turkey, however, still imports some cotton fabric from China (approximately 23% in 2018).
Trade tensions between Turkey and China and talks of limiting Chinese textiles have contributed to decreased imports from China. Turkey may present a near-term option for reshoring for the EU market, especially if concerns about state-sponsored forced labour in inputs from Turkmenistan and Uzbekistan can be addressed.
East and West Africa
Both present long-term opportunities to develop vertically integrated supply chain hubs. However, this will take considerable time and require appropriate investments in capacity and infrastructure from other governments and commitments from brands to source from the region to encourage yarn and textile manufacturers to migrate there.
Africa is also a significant producer of cotton, with four major cotton zones located in a vertical strip from Egypt to South Africa and a major basin in West Africa. In particular, West Africa, which produces about 5% of the world’s cotton (two-thirds of Africa’s total output), has significant capacity to scale up production. Cotton yields in Africa are low, which presents an opportunity to increase production by improving seed availability, agricultural techniques (such as irrigation and fertilisation), and region-wide capacity building.
If cotton yield rates in West Africa (Burkina Faso, Chad, Mali, and Senegal) were as high as yield rates in China, West Africa alone could produce as much as 10m metric tonnes of cotton – significantly more than China’s forecast cotton production in 2018–2019 (5.9m metric tonnes).
The current lack of textile manufacturing capacity presents a bottleneck for Africa’s cotton, textile, and apparel value chain. Currently, Africa sources much of its textiles from China and other Asian countries, with China contributing to over 40% of total textile imports to sub-Saharan Africa. Textile firms – primarily of Chinese origin – have been interested in investing in the textile industry in Africa, with a potential investment pool estimated to be over $300m. This creates a risk that XUAR raw cotton will simply shift to Africa, although this is only a risk if demand for XUAR raw cotton dries up in China. However, some research suggests that these Chinese firms are often not state-backed, may cooperate in designing labour and environmental standards, and may be willing to follow customers’ directions about the origin of the yarn and cotton they use.
The sense in diversification
“The regions discussed above present different challenges as well as opportunities for sourcing. It is unlikely that any particular country or region will fully replace China as the next major sourcing hub. In fact, it is likely that multiple regions may be developed for different purposes,” the report states.
“Scaling up is likely to be fastest in countries and regions where there is already some vertical integration.
“Scaling up is likely to be fastest in countries and regions where there is already some vertical integration. Companies and governments could jointly target key Asian countries such as Vietnam, India, Bangladesh or Indonesia for larger-scale and more technical production.
“Central America and Mexico might play niche sourcing roles in certain product categories for the North American market, taking into account limitations on producing highly technical products. Turkey might play a similar nearshoring role for the EU market, with greater technical capacity.The United States and European Union could both develop longer-term plans to support vertical integration in African supply chains.
“All of these efforts should incorporate strong social and environmental safeguards as a priority so that alternative sourcing hubs are more responsible and thus a meaningful improvement on the status quo.
“Diversification requires coordination from multiple actors, including governments, companies, international organisations, NGOs, and other country-level stakeholders. Diversification is valuable in its own right and may help create pressure to change practices in the XUAR. Because of the challenges that will likely arise, diversification efforts must start now.”
Click here for the full report from CSIS.