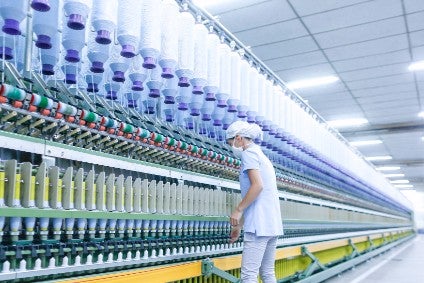
For all the talk of China’s weakening role as a global apparel supplier, one thing’s for sure: it looks set to continue its dominance of the international textile industry. Indeed, new data shows the country remained the world’s largest investor in spinning, texturing, weaving and knitting machinery last year.
Trends in upstream spinning, weaving and knitting machinery investments are an important indicator of future sources of textile production, as well as helping to benchmark those countries where new, modern equipment can drive better efficiency, quality, lower production costs and more environmentally-friendly production.
And the annual survey of International Textile Machinery Shipment Statistics provides a key snapshot of the top countries building capacity in fibre, yarn and fabric supply.
Global deliveries of new short-staple spindles and open-end rotors edged up by 1.5% and 13% respectively year-on-year in 2018, according to data released by the International Textile Manufacturers Federation (ITMF). But growth was considerably slower than the previous period from 2016 to 2017, when shipments of new short-staple spindles were up 21%, long-staple spindles jumped 46%, and open-end rotors rose by 24%.
Meanwhile, the number of draw-texturing spindles shipped last year rose by 50% and deliveries of shuttle-less looms were up by 39%.
In contrast, shipments of long-staple spindles were down 27%, circular knitting machines fell 4%, and electronic flat knitting machines decreased by 20%. And in the finishing segment, total machines shipped worldwide in the ‘fabric continuous’ category were down 0.5%, while those classified as ‘fabric discontinuous’ fell by 1.5% year-on-year.
How well do you really know your competitors?
Access the most comprehensive Company Profiles on the market, powered by GlobalData. Save hours of research. Gain competitive edge.
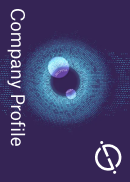
Thank you!
Your download email will arrive shortly
Not ready to buy yet? Download a free sample
We are confident about the unique quality of our Company Profiles. However, we want you to make the most beneficial decision for your business, so we offer a free sample that you can download by submitting the below form
By GlobalDataThe 2018 survey was compiled in cooperation with more than 200 textile machinery manufacturers.
Spinning machinery
The total number of shipped short-staple spindles increased by about 126,000 units to a level of 8.66m. Shipments increased for the second consecutive year, but the global trend slowed.
Most of the new short-staple spindles (92%) were shipped to Asia and Oceania, although delivery fell by 2%. The six largest investors in the short-staple segment were China, India, Uzbekistan, Vietnam, Bangladesh and Indonesia. And the most dynamic destinations recorded in 2018 were South Korea (up 834%), Turkey (up 306%), Vietnam (up 290%) and Egypt (up 285%).
Global shipments of long-staple (wool) spindles dropped from 165,000 in 2017 to around 120,000 in 2018, mainly due to a drop in Asia and Oceania where the number of units delivered fell by 48,000. This region remained the strongest destination for this type of machinery but deliveries to China and Iran dropped by 60%. Even so, the biggest investors were Turkey, Iran, China, Italy and Vietnam.
According to the survey, 721,000 open-end rotors were shipped worldwide in 2018. This represents a rise of 83,000 units on the year before. 91% of the global shipments went to Asia and Oceania where the share of total deliveries improved by 20% to 658,000 rotors. China, the world’s largest investor in open-end rotors, increased its purchases by 7% in 2018, while deliveries to Thailand, Malaysia, and Egypt rose three-fold.
Texturing machinery
Global shipments of single heater draw-texturing spindles (mainly used for polyamide filaments) increased by 48% from nearly 15,500 in 2017 to 22,800 in 2018. With a share of 91%, Asia and Oceania was the strongest destination for single heater draw-texturing spindles. China and Japan were the main investors in this segment with a share of 68% and 11% of global deliveries, respectively.
In the category of double heater draw-texturing spindles (mainly used for polyester filaments) the positive trend continues with global shipments increasing by 50% on an annual basis to about 490,000 spindles. Asia’s share of worldwide shipments grew to 93%. China again remained the largest investor accounting for 68% of global shipments.
Weaving machinery
In 2018, worldwide shipments of shuttle-less looms increased by 39% to 133,500 units. Deliveries of air-jet looms increased by 21% to 32,750, and water-jet looms soared by 91% to 69,240. But deliveries of rapier/projectile looms fell by 5% to 31,560.
The main destination for shuttle-less looms in 2018 was Asia and Oceania with 93% of all worldwide deliveries. 92% of all water-jet looms, 83% of all rapier/projectile looms, and 99% of all air-jet looms went to that region. The main investors were China and India in all three categories.
Deliveries of weaving machines to the two countries reached 81% of total deliveries. Turkey and Bangladesh also played an important role in the rapier/projectile segment with a combined 18% of global shipments.
Circular and flat knitting machinery
Global shipments of large circular knitting machines fell by 4% to 26,300 units in 2018 – with Asia and Oceania again the world’s leading investor in this category with 85% of all new circular knitting machines shipped to the region. With 48% of worldwide deliveries, China was the largest investor. India and Vietnam ranked second and third with 2,680 and 1,440 units, respectively.
Deliveries of electronic flat knitting machines were also down, falling by 20% to around 160,000 machines. Asia and Oceania was the main destination for these machines with a share of 95% of world shipments. China remained the world’s largest investor. The country kept its global share of 86% of worldwide shipments despite a drop in investments from 154,850 units to 122,550 units.
Finishing machinery
In the segment of ‘fabrics continuous,’ shipments were up for washing (stand-alone) (up 58%), singeing line (up 20%), relax dryers/tumblers (up 9%), stenters (up 3%) and sanforizers/compacters (up 1%). Deliveries in the other sub-segments decreased. In ‘fabrics discontinuous,’ shipments of air-jet dyeing machines increased by 16% and deliveries of overflow dyeing and jigger dyeing/beam dyeing machines fell 7% and 19% respectively.
Facts behind the figures
China’s stranglehold on world textile trade is undisputed. Not only is it the world’s largest producer of fibre and fabric – accounting for more than half (54.8%) of global production in 2017 – but it is also the largest textile exporter, with shipments that same year reaching US$109.9bn and taking 37.1% of the global total.
China also exported apparel worth US$158.4bn in 2017, giving it a 34.9% share of the world market – and the top share in the world’s three largest apparel importers: the US, EU and Japan.
Much of this strength is due to the size of its supply base, its range of skills, its quality levels, its product variety – and the completeness of its supply chain from raw materials through to fabrics, dyeing, finishing and final products.
Growth has also been helped by investment into upstream textile plants where new, modern equipment is driving better efficiency and quality, along with lower production costs – as well as enabling China’s mills to offset the pressure of increasingly stringent environmental regulations.
Initiatives from the Chinese government such as ‘Made in China 2025’ and the 13th Five-Year Plan for the Textile Industry (covering the period from 2016-2020) are also putting a strong focus on value-added manufacturing and automation, which in turn supports investment into upstream textile plants.
But there are also subtle shifts at play. The competitiveness of China’s apparel exports is weakening – a trend exacerbated by ongoing trade tensions with the US and concerns over the likelihood of additional tariffs on textile and clothing imports. While at the same time, China’s share of world textile exports is growing, fuelled by growing demand from many apparel exporting countries in Asia.
Measured by value, 47% of Bangladesh’s textile imports came from China in 2017, up from 39% in 2005. Similar trends are seen in Cambodia (up from 30% to 65%), Vietnam (up from 23% to 50%), Pakistan (up from 32% to 71%), Malaysia (up from 25% to 54%), Indonesia (up from 28% to 46%), Philippines (up from 19% to 41%) and Sri Lanka (up from 15% to 39%) over the same period.
This is partly due to the emergence of more regional patterns in world textile and apparel trade and production networks, with an analysis on just-style noting that close to 80% of textile imports within Asia came from within the region in 2017.
“With their relatively lower wages, the less developed countries typically undertake the most labour-intensive apparel manufacturing processes,” explains author Dr Sheng Lu, associate professor in the University of Delaware Department of Fashion & Apparel Studies. “In addition, various regional free trade agreements – such as the ASEAN-China Free Trade Agreement and the ASEAN-Japan Comprehensive Economic Partnership Agreement – have also helped through the elimination of tariff and non-tariff barriers.”
The shifting sourcing strategies of fashion brands and retailers as they move orders to diversify their supply bases are also at play. A recent survey found 83% of US fashion companies plan to reduce their sourcing from China over the next two years due to concerns over the threat of new tariffs – with the main beneficiaries being other suppliers in Asia.
But much textile investment around the world is still being funded by Chinese firms – who are leading the way when it comes to expanding raw material production and processing overseas. This outward investment helps ensure stable supplies, as well as enabling them to tap into lower labour and energy costs, and benefit from preferential rules of origin within free trade arrangements.
In 2016, the foreign direct investment (FDI) of the Chinese textile industry hit a record high, up 89.3% year-on-year to US$2.66bn. According to statistics from the Ministry of Commerce, by the end of 2014 more than 2,600 Chinese companies had opened textile and apparel production facilities in more than 100 countries and regions, with most investment going to Asia.
China’s role in global textile supply chains is shifting in other ways too.
The country is emerging as one of the world’s largest consumer markets – and the majority of garments bought in China are made in China from fabric knitted or woven in China. Which means that much of its current and future textile machinery investment is likely to focus on meeting demand from its own domestic customers – and may lead to competition for the export production capacity demanded by Western brands and retailers and other Asian suppliers.
Vietnam investments
Competition for export production capacity means that another machinery investment trend to watch is in Vietnam, where apparel exports are growing but factories are increasingly stressed about fulfilling additional orders due to a shortage of local raw materials.
Over 60% of fabrics needed by Vietnamese garment manufacturers still have to be imported, yet interest in the country is on the rise thanks to its participation in two major new trade deals: the Comprehensive and Progressive Agreement for Trans-Pacific Partnership (CPTPP) and the EU-Vietnam Free Trade Agreement (EVFTA).
The CPTPP entered into force for Vietnam in January 2019, incrementally bringing down import tariffs for Vietnamese garments traded with signatories Australia, Brunei, Canada, Chile, Japan, Malaysia, Mexico, New Zealand, Peru and Singapore. But its yarn-forward textile rules of origin mean each component – from spinning the yarn, to weaving or knitting the fabric, and making the garments – must take place within the free trade area in order to qualify for duty-free treatment.
With weak local backward linkages, Vietnamese garment factories currently have to import the majority of the materials they need from non-CPTPP member nations. Changes are afoot though, with fabric investments starting to strengthen – and potential policy changes to encourage domestic textile production.