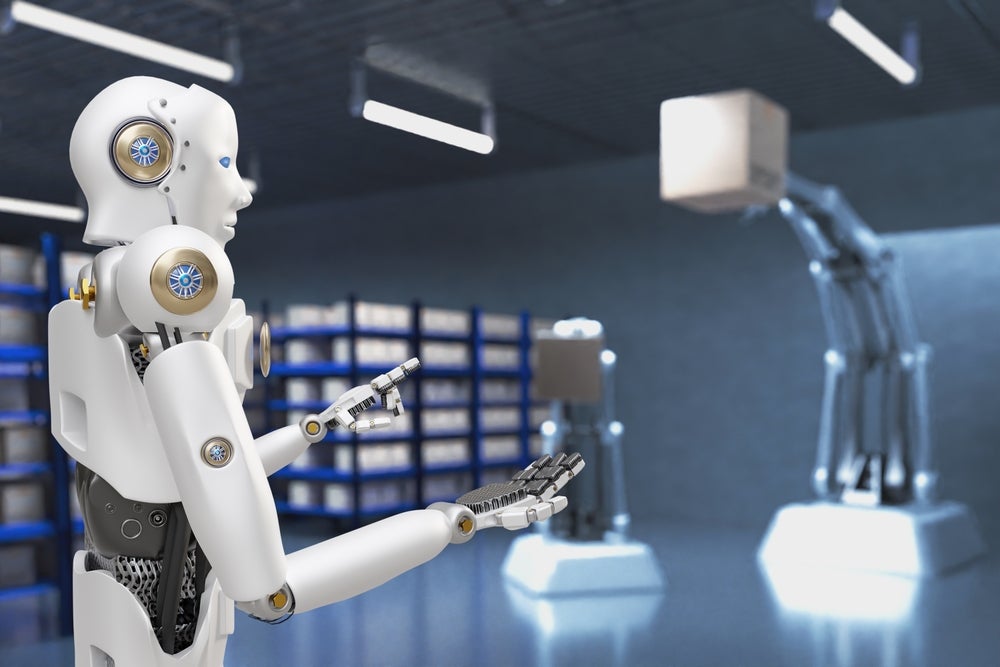
Smartex’s report titled ‘The Modern Textile Factory’ says the status quo of how an apparel factory is run will not serve the purposes of either financial growth or impact reduction.
The report, which was authored by Smartex’s global innovation director Max Easton reads: “The joint incentives for modernisation of a commercial carrot and a regulatory stick provide an impetus for change. This confluence allows a rare handshake between advocates of a more sustainable textile industry and pure-profit seeking brand owners. The enabler for both sustainability and greater economic strength for both brands and suppliers is the same: a supply chain fulfilled by Modern Textile Factories.”
However, Smartex admitted there are challenges and modernising textiles factories is not a quick or easy endeavour.
It advised suppliers to radically prioritise their limited investment bets as the textile
supply chain has tight margins, limited budgets and a need for quick returns on
investments.
Smartex added this “is primarily because fashion brands are unforgiving on price increases and will switch suppliers without a second thought. Factories are driven by a defensive mindset because of the uncertainty in their customer relationships”.
The report pointed out apparel factories need to be supported by technology companies with simple, effective and cost-efficient innovations and brands need to provide financing and longer-term relationships to allow the leading factories to not just survive, but thrive.
Crucially, Smartex said apparel factories need to start modernising now, not in the future – or risk becoming obsolete.
Smartex believes that without what it calls “Modern Textile Factories’, consumers, brands, investors and legislators will be in for a big shock as:
- Technology companies with genuinely more sustainable materials and processing improvements will struggle for adoption in an analogue supply chain
- Brands will continue to have an incomplete and outdated understanding of their supply chains, including their share of factory emissions or the particular inputs and processes used on their products
- Investors will struggle to scale technology companies in the space, hold large brands accountable or understand the risks of their portfolio
- Legislators will struggle to incentivise market change because poor, inaccurate and slow data reporting means they can’t tax externalities effectively (e.g. carbon tax).
- The textile industry’s approximate contribution of 2% of global emissions won’t really reduce – and may actually increase as a percentage as other industries decarbonize more quickly.
Smartex’s five pillars for a modern apparel factory in 2024
Smartex outlined five key elements to creating a successful and modern apparel factory in 2024:
- Resource efficiency
Reduced cost, higher profits, reduced emissions. Smartex said this is ESG capitalism’s dream with one brand stating that anything that reduces wastage “is an easy implementation as everyone wins”. Modern Textile Factories will continually
seek to improve their resource efficiency to lower their cost and the environmental impact of each unit produced.
2. Real-time data collection
For suppliers to stay competitive on speed, quality, price and compliance, objective,
verifiable and real-time data is key. Smartex calls this type of data ‘golden
data as it enables an accurate understanding of the full cost of a product, a factory’s free capacity, clear quality metrics and environmental and social impact. In a lot of ways, this is the first domino that needs to fall in a factory’s modernisation journey since it is a key enabler for improvement.
3. Data-driven decision making
Once data is available, decision-making needs to switch from traditional to fact-based. Pen and paper textile factories are known for believing in the “tried-and-tested method”. For example, operators are certain that their machines must run at certain speeds or settings “because that’s the way it has always been done”.
However, in an era of balancing revenue-generating speed with quality-dependent
profits, technology is a more reliable compass. Using data to make decisions
will be a recurring theme within the best factories.
4. Integration with stakeholders
There is no benefit to working in silos. Factories need to understand what they’re
buying (quality, quantity, material, origin) to most effectively process it and
send it on – enriched both physically and digitally – to their customers.
This is certainly a strength of vertically integrated facilities, which can connect
more easily with other supply chain steps by linking up factory systems. As a result, they can have full visibility on the production process to review order progress, identify problem areas and continuously improve.
5. High quality, safe jobs
Modern Textile Factories will be safe, nontoxic and innovative places to work. What is considered the status quo today will seem a relic of history in Modern Textile Factories.
Factory workers will work closely with smart machinery to achieve fast, efficient
and high quality results. As a result of technology progression, workers will require
constant training and upskilling to maximise the factory’s investment in technology and deliver products with the right mix of price, speed, quality and compliance.